Back in 2014 one of the projects I worked on was part of the Oregon Manifest design challenge, a recurring bike design competition that my client Ti Cycles was participating in. As a way of freshening up the event format the 2014 edition paired bike industry professionals with cutting edge design firms and then turned them loose on the theme of “the ultimate commuter bike.”
The Oregon-based team really swung for the fences. The designers at INDUSTRY were a forward thinking bunch, the Ti Cycles shop is known for specializing in titanium, and coincidentally one of the country’s first commercial titanium printers was just up the river at I3D. The collaboration ultimately rendered SOLID, the world’s first 3D printed titanium bike, which in spite of not winning the design competition did have its 15 minutes of internet fame.
During that time I fielded 5 Questions from Faith Robinson as part of the UK’s 3DPrintShow. Images courtesy of IndustryPDX.
Why is it important to be able to offer customized items, like bicycles?
The demand for custom bicycles has existed more or less as long as the bicycle. Production bicycle size fit some people, but certainly not everyone.
As anyone who has ridden an improperly fit bike can attest, it doesn't take long for a bad fit to manifest itself in knee pain, wrist pain, back pain, et cetera. That pain can at the least ruin a ride and turn someone off to cycling, and at the worst lead to injury. To a certain extent cockpit components can alleviate some fit issues, but in many cases the available off the shelf frames or parts just will not work.
Biomechanics and fit aside, there’s a reason that bone stock articles of anything of any vintage are hard to find; be it bicycles or automobiles, Craftsman houses or cave walls, personalization has always been a part of human nature.
3D printing technology has proved itself to be incredibly well suited to creating one-off items. What is your opinion towards 3D printing in terms of facilitating this?
In many ways 3D printing is ideal for one-off or custom items. The SOLID bike's fork crown, for example, is not something we could easily make with traditional methods.
Tell us about your Solid collaboration with design consultancy INDUSTRY. How did it come about?
All of the design firms and frame builders were invited to participate by Oregon Manifest. There are two ways to approach collaboration -- put two minds together until they reach consensus, or take ideas from one and allow the other to riff on them. SOLID was the latter; Industry took the existing SuperCommuter platform and ran with it, coming up with a new design that is a clear separation from the Ti Cycles aesthetic.
The Oregon Manifest design competition theme is the commuter bicycle, and Industry definitely took that idea into the future -- especially with the electronics suite on the bike and connected app – while incorporating a number of Dave's signature elements like the monostay rear end, the chainstay frame break, and the integrated bar/stem combo.
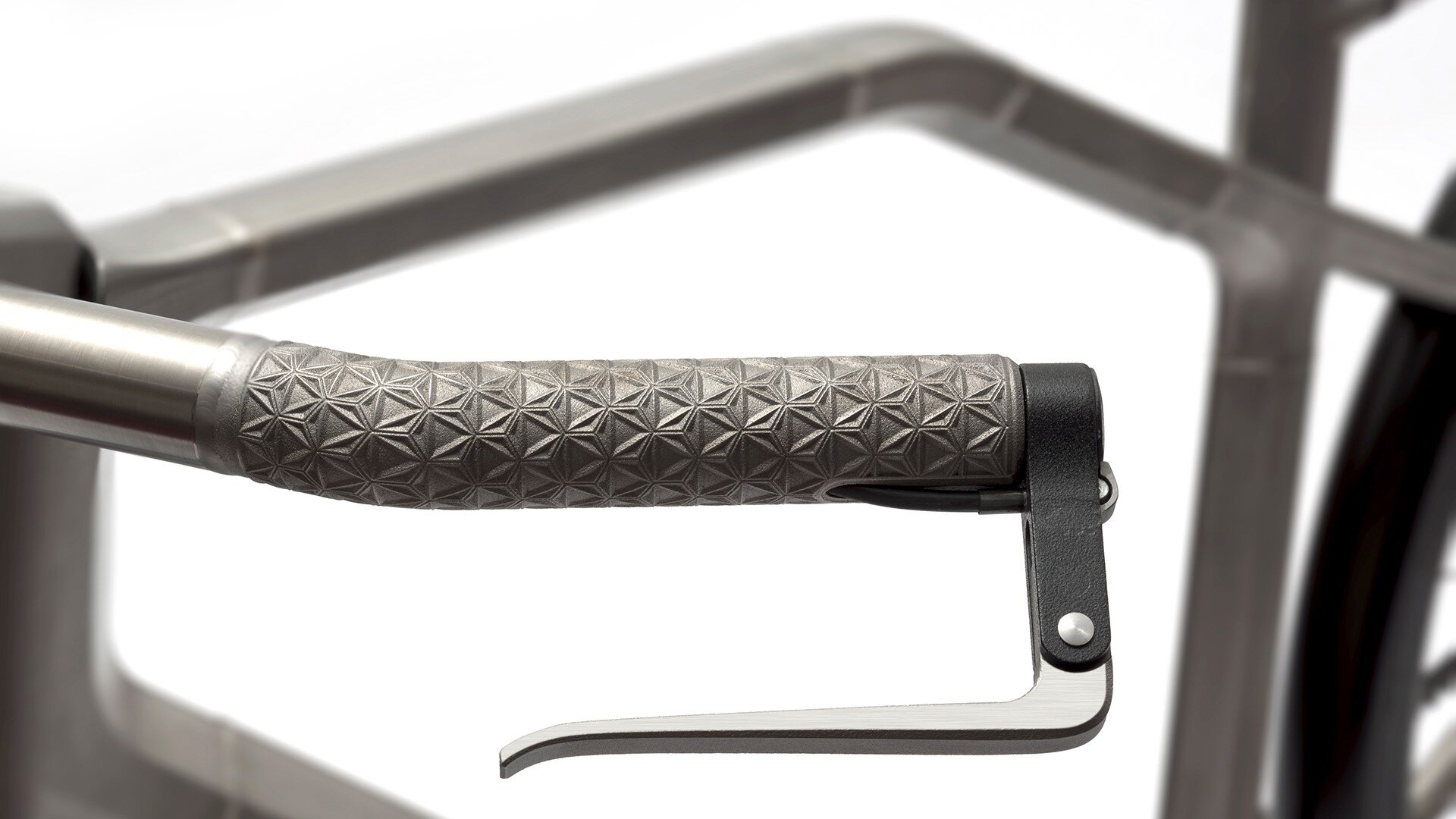
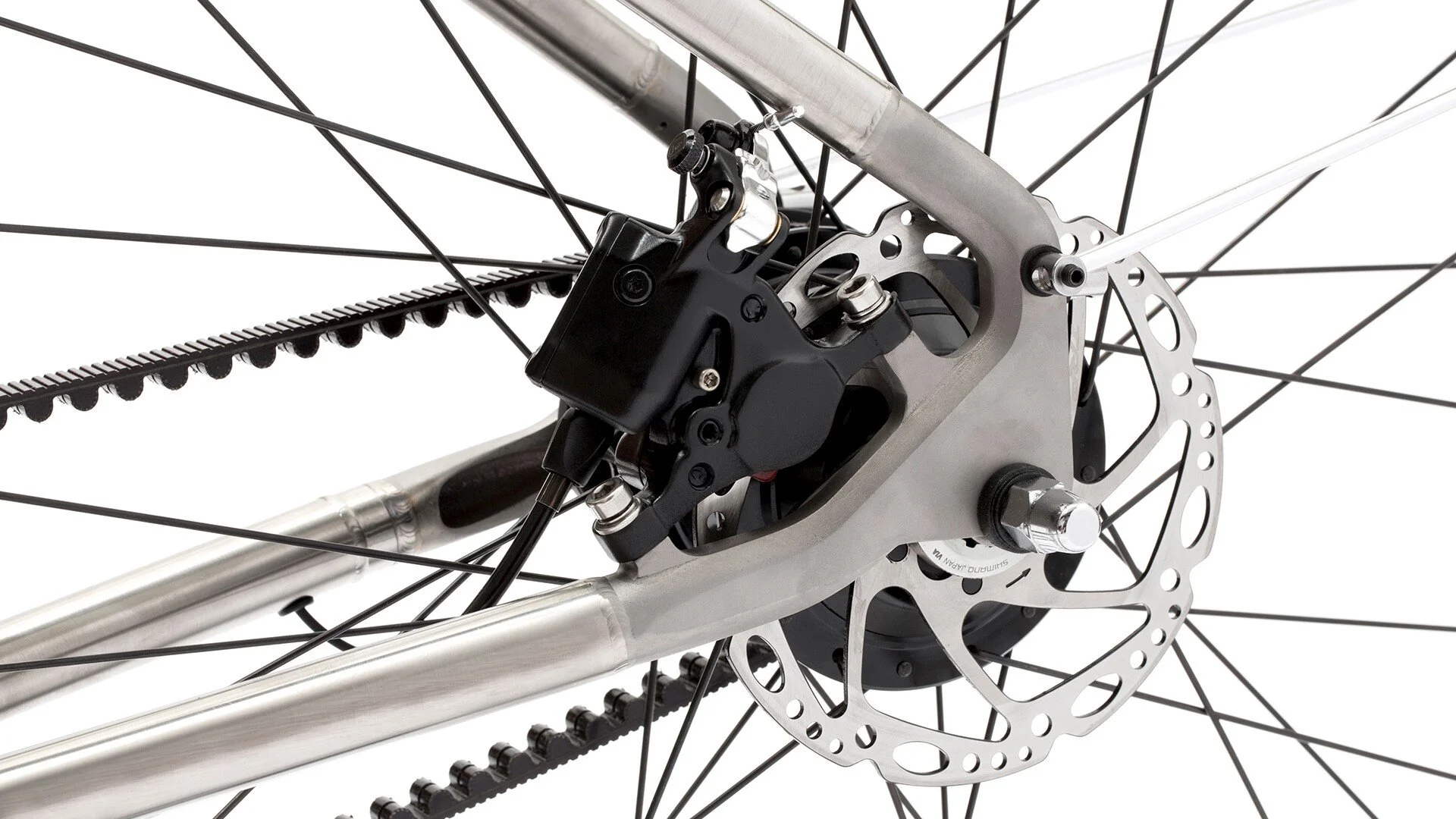
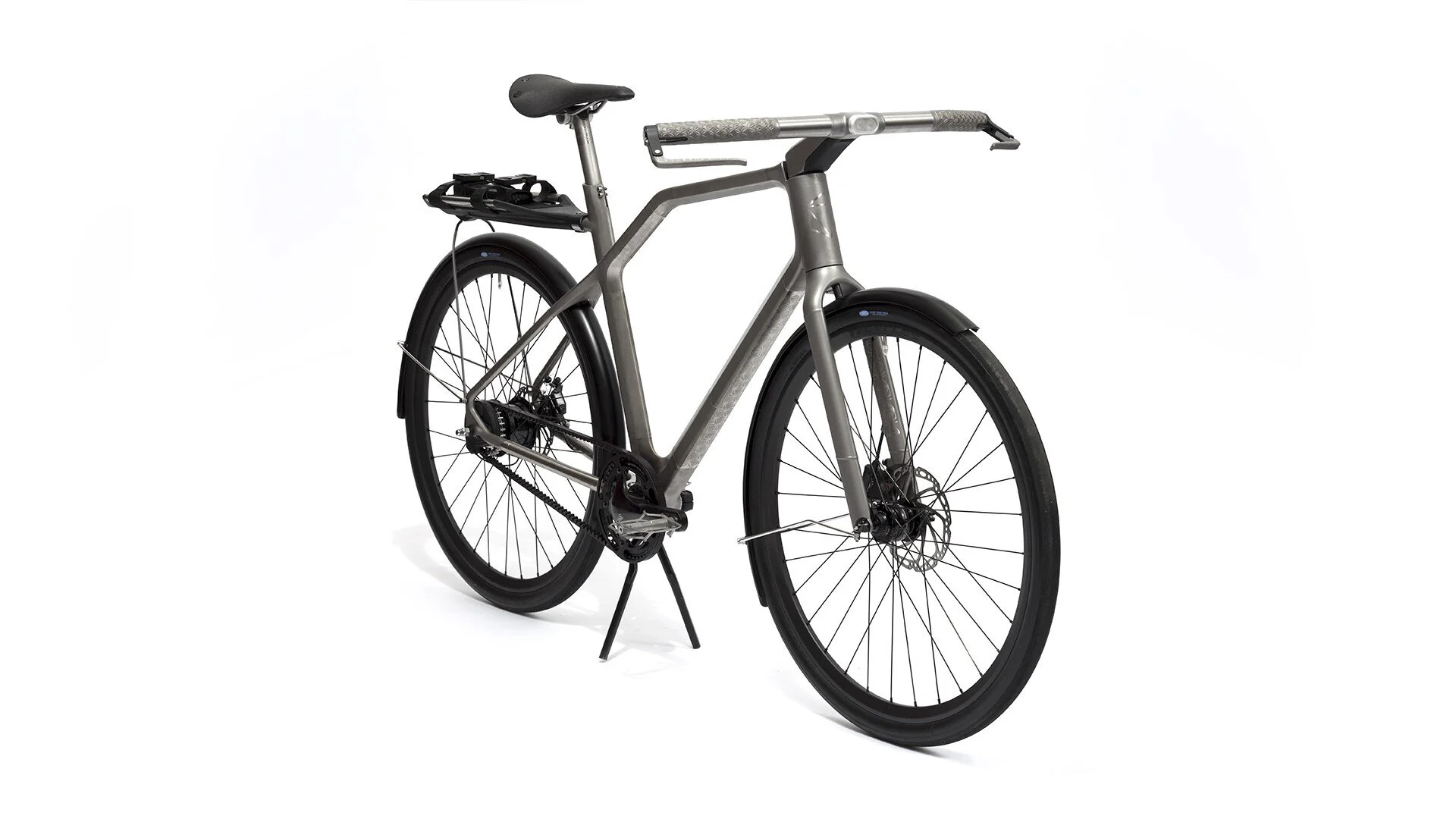
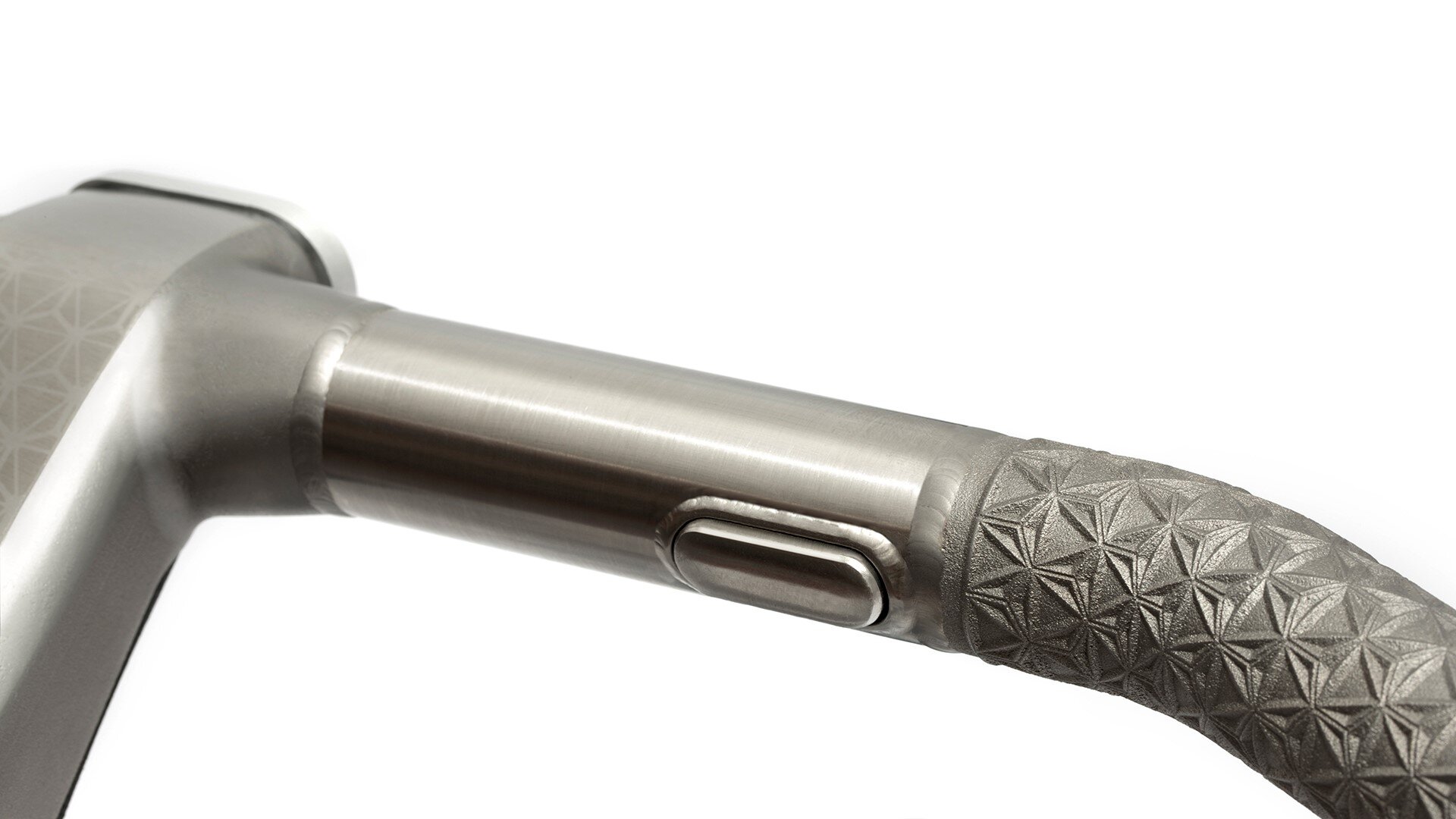

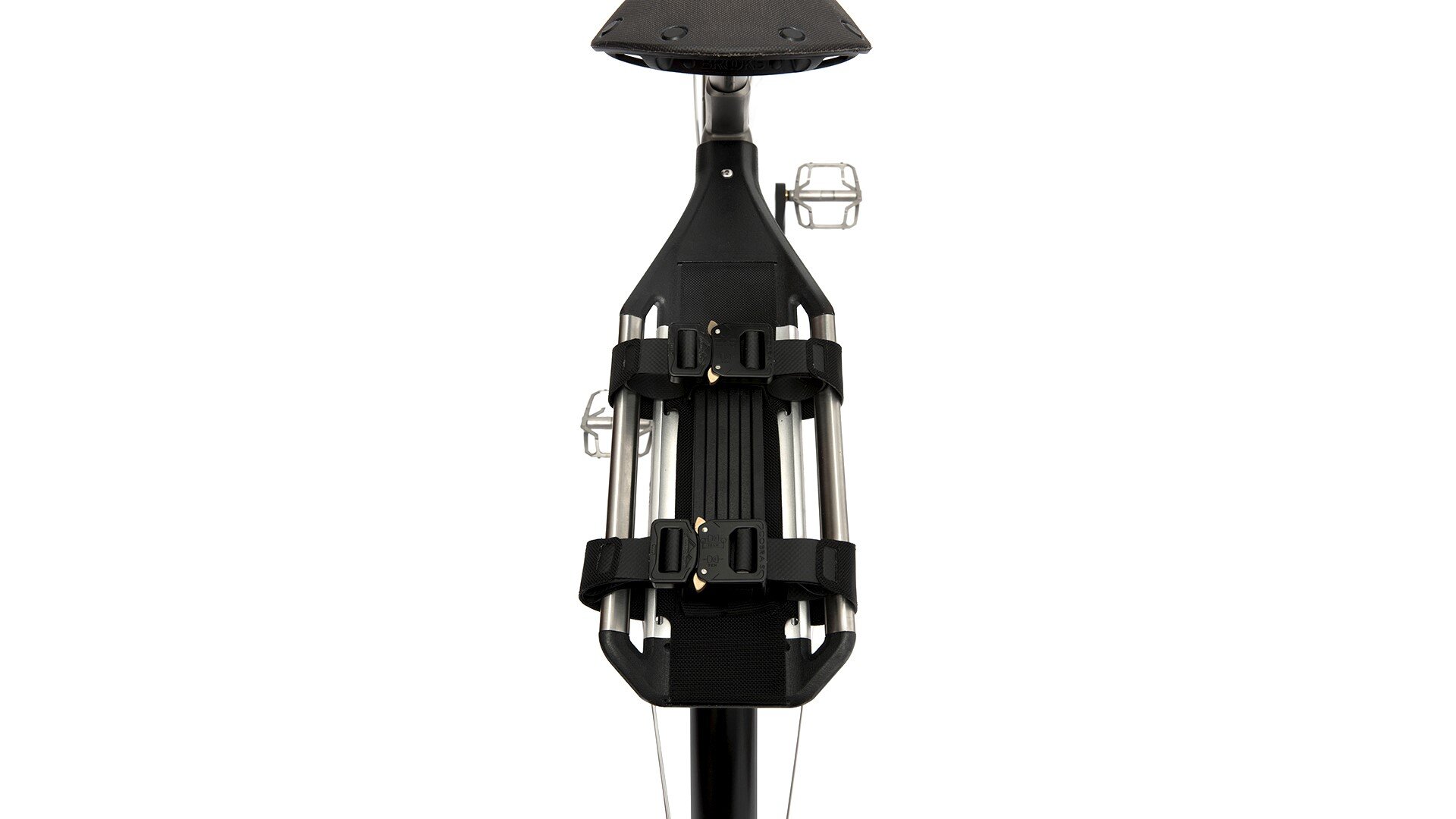
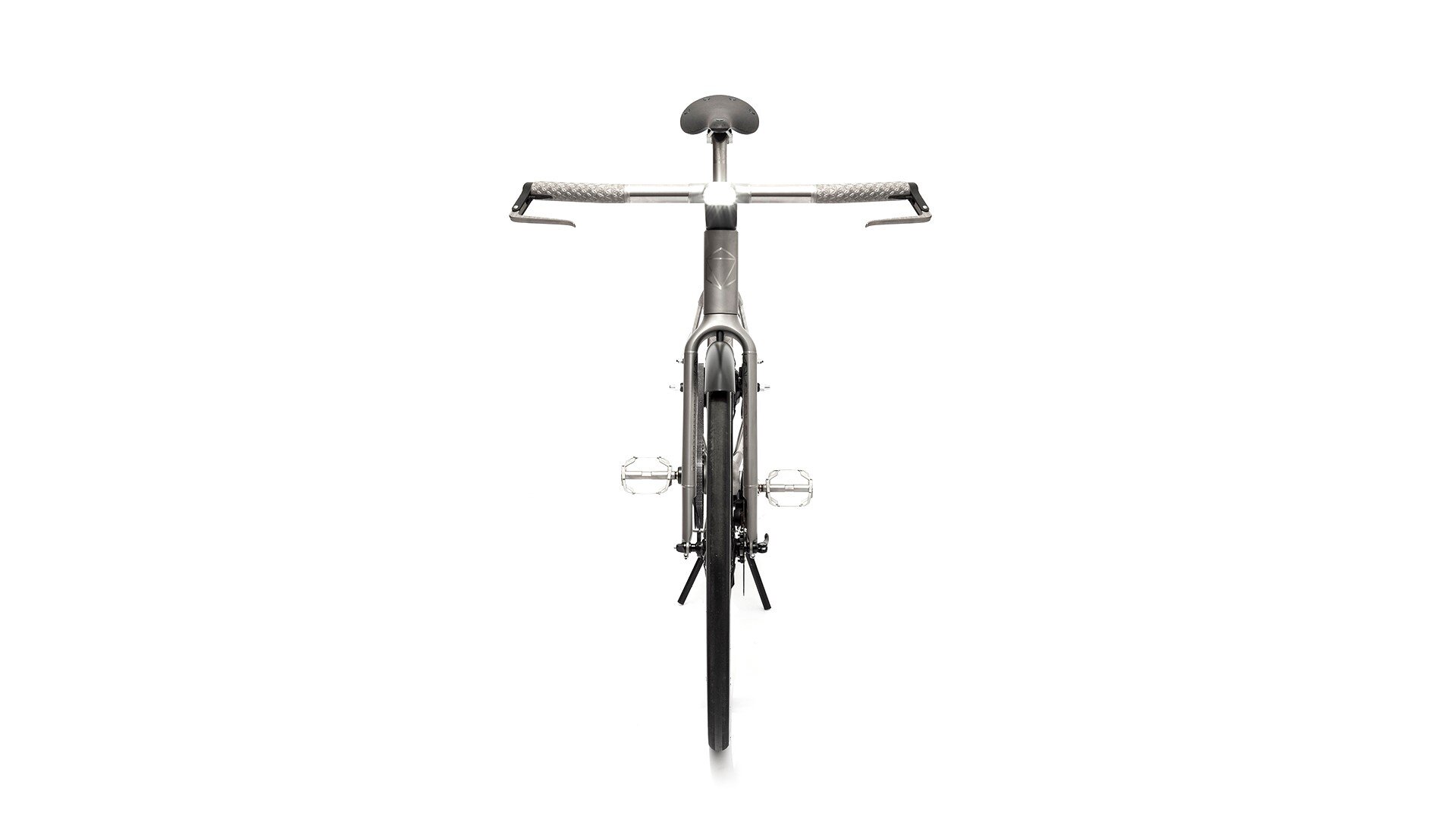
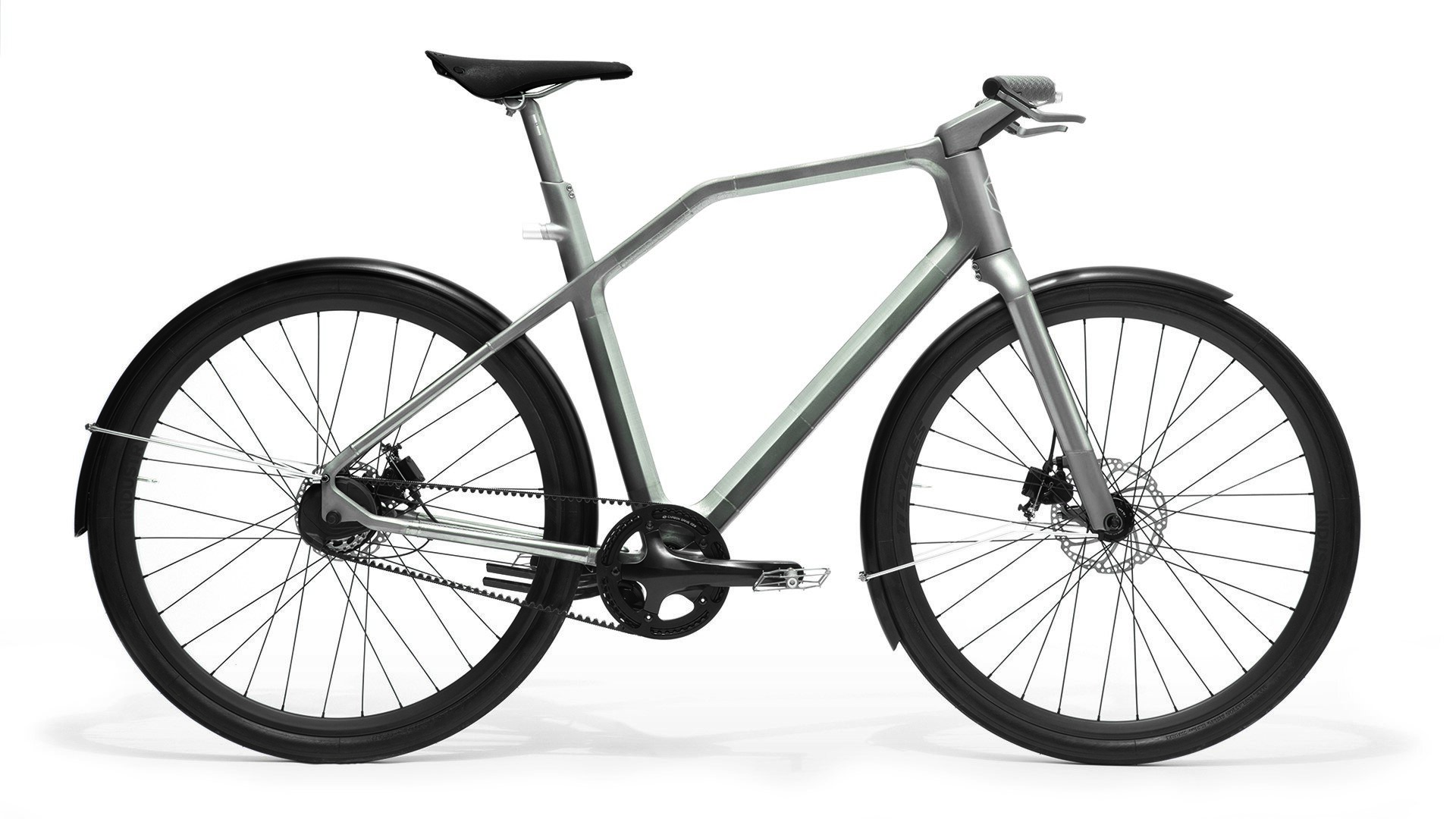
Why was titanium the material of choice for this 3D printed bicycle?
One of the six key ingredients of a SuperCommuter is the titanium frame. We love steel bikes and continue to build them every year, but a bike is not a SuperCommuter if it can rust away in the wrong environment or come unglued.
Do you see a future for the development of this kind of production method?
When you see the parts that I3D can produce there is no question that 3D printing is the future. In 2014 it is very much in its infancy but such a fantastic technology! In particular with titanium but also with other materials, right now it is far too cost and scale prohibitive to do any real manufacturing. The tycoon who needs a new wobblygog for his yacht will be served well by this technology years before the rest of us. Ti Cycles turns 25 in 2015; my guess is that there'll be at least another 25 years of world class, hand crafted titanium and steel bikes before very many bikes are made from dust and lasers.